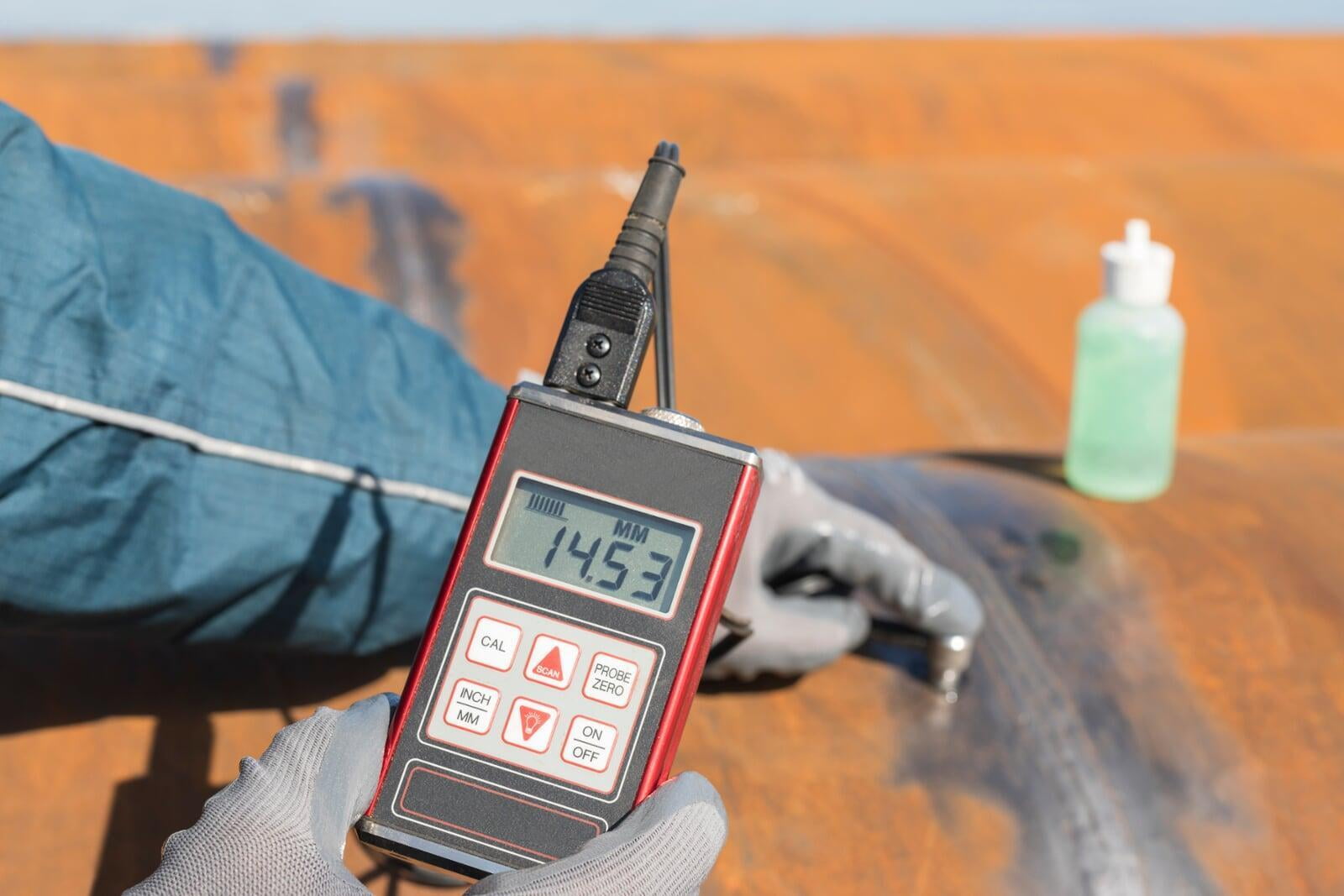
Corrosion Detection
IECM can be used to analyze data from the pipeline to better detect corrosion, providing early warning of potential problems and allowing for timely repairs.
Corrosion is a significant issue for pipelines and other metal structures, which can lead to leaks, failures, and significant safety risks. To prevent these problems, it is essential to monitor pipelines continuously and detect any signs of corrosion before it causes significant damage. Fortunately, advances in technology have made it possible to analyze data from pipelines to better detect corrosion, providing early warning of potential problems and allowing for timely repairs.
The first step in detecting corrosion is to monitor the pipeline's condition continually. This can be done using a range of sensors, including ultrasonic sensors, electrochemical sensors, and magnetic flux leakage sensors. These sensors can detect changes in the pipeline's thickness, internal pressure, and other factors that could indicate corrosion. The data from these sensors can be transmitted in real-time to a central monitoring system, where it can be analyzed and used to make informed decisions about maintenance and repairs.
Once the data has been collected, it can be analyzed to identify any areas of concern. This can involve comparing the data from different sensors to look for discrepancies or using predictive modeling to identify areas that are likely to experience corrosion in the future. For example, machine learning algorithms can analyze large datasets to identify patterns that may be associated with corrosion, allowing engineers to predict which areas are most likely to experience problems in the future. Mechanistic models on the other hand utilizes rectifier outputs as input for the current density and potential distribution computations along the full pipeline length. The current density is directly correlated to the corrosion rate. Coating surveys such as DCVG/ACVG and ILI anomaly features provide semi-quantitative information on the coating defect size such that current densities are computed more accurately. For each computation the instantaneous corrosion rate is obtained, as well as the corrosion growth rate over time if computations are repeated based on updated sensor and survey data.
Another approach to corrosion detection is to use non-destructive testing techniques to inspect the pipeline's surface. These techniques include visual inspection, ultrasonic testing, magnetic particle testing, and radiography. By using these techniques, engineers can identify areas of corrosion before they become significant problems, allowing for timely repairs and preventing leaks or failures.
One of the challenges of corrosion detection is that pipelines are often located in remote or hazardous areas, making it difficult to perform regular maintenance and inspections. However, advances in remote sensing technology have made it possible to monitor pipelines from a distance. For example, drones can be equipped with sensors to inspect pipelines from the air, while autonomous robots can be used to inspect pipelines in areas that are difficult or dangerous for humans to access.
In conclusion, corrosion detection is essential for maintaining the safety and integrity of pipelines and other metal structures. By analyzing data from pipelines and using advanced sensing and inspection techniques, engineers can detect corrosion early and prevent significant problems from occurring. As technology continues to advance, it is likely that corrosion detection will become even more effective, allowing for safer and more reliable pipelines in the future.