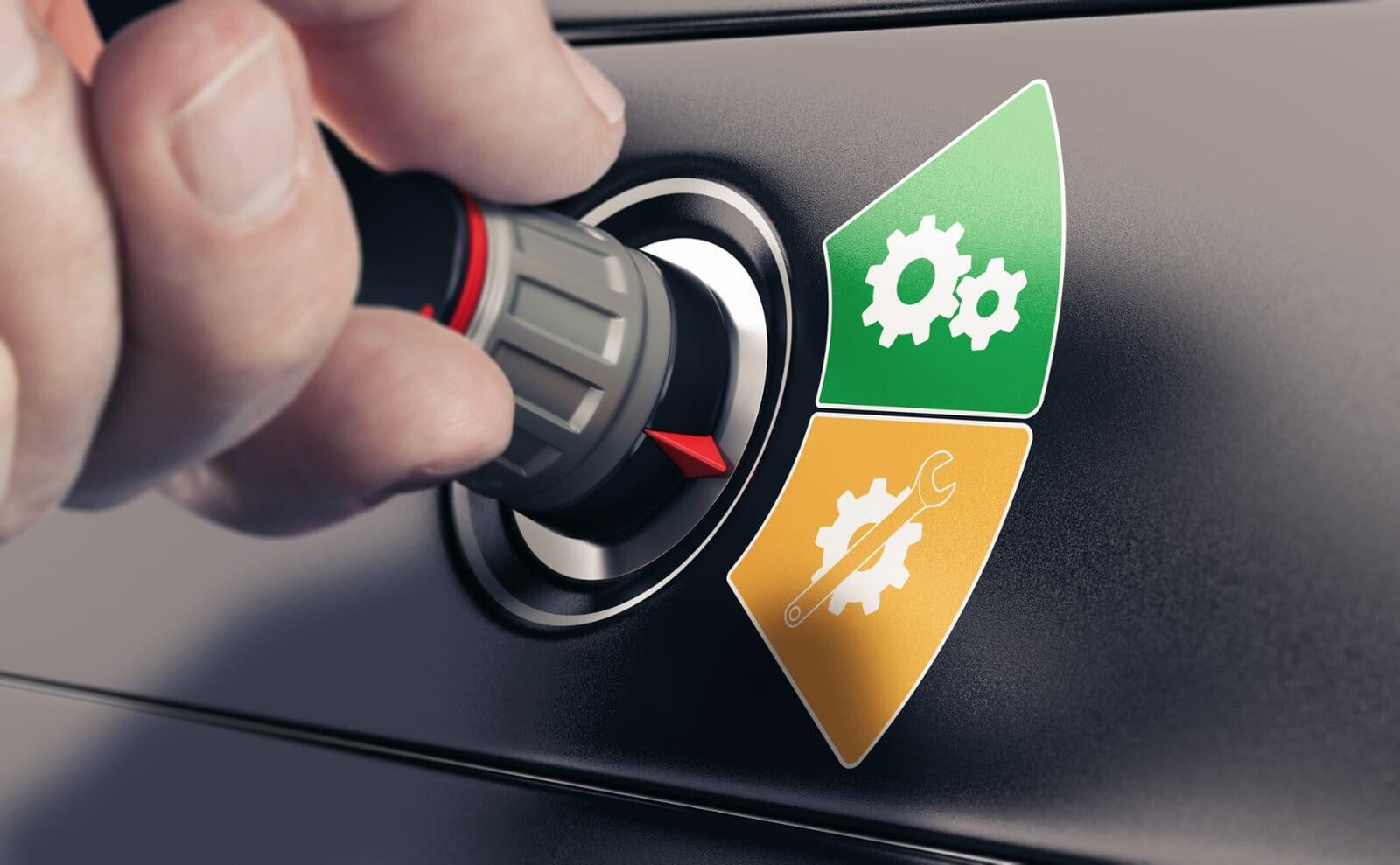
Predictive Maintenance
IECM data can be used to analyze data from corrosion monitoring systems and predict when maintenance is needed, reducing downtime and increasing efficiency.
The maintenance of underground pipelines is a complex and often challenging task that requires careful monitoring and planning. Corrosion is a significant issue for pipelines, and detecting it early is essential to prevent leaks, failures, and safety risks. Fortunately, advances in technology have made it possible to use predictive maintenance data to analyze data from corrosion monitoring systems and predict when maintenance is needed, reducing downtime and increasing efficiency.
Predictive maintenance involves using data and analytics to predict when maintenance is required before any issues occur. This approach allows maintenance to be scheduled at optimal times, reducing downtime and increasing efficiency. For underground pipelines, predictive maintenance can be especially challenging, as access to the pipeline is often limited, and detecting potential problems early can be difficult.
However, by using corrosion monitoring systems, it is possible to collect data on the pipeline's condition continually. This data can be analyzed using predictive maintenance algorithms to identify potential issues before they become significant problems. For example, machine learning algorithms can analyze large datasets to identify patterns that may be associated with corrosion, allowing engineers to predict when maintenance is needed. Or mechanistic models can predict the impact of unintended events on pipeline’s corrosion. The increase in corrosion rate due to a rectifier outage or a disconnect of a bond between pipelines is computed and priorities defined .
One of the benefits of using predictive maintenance for underground pipelines is that it allows maintenance to be scheduled at optimal times. This can help to reduce downtime and increase efficiency, as maintenance can be performed when it is least likely to disrupt operations. Additionally, by detecting potential issues early, predictive maintenance can help to prevent significant problems from occurring, reducing the risk of leaks or failures and improving safety.
To implement predictive maintenance for underground pipelines, it is essential to have a comprehensive corrosion monitoring system in place. This system should include a range of sensors, including ultrasonic sensors, electrochemical sensors, and magnetic flux leakage sensors. These sensors should be placed at strategic locations along the pipeline to monitor its condition continually.
Most strategic locations for installing such devices are determined by simulating events that adversely impact the pipeline’s corrosion condition.
The data collected by these sensors should be transmitted in real-time to a central monitoring system, where it can be analyzed using predictive maintenance algorithms. These algorithms should be designed to identify potential issues based on the data collected by the sensors and provide recommendations on when maintenance should be performed.
In conclusion, predictive maintenance is an effective approach to maintaining underground pipelines. By using data and analytics to analyze data from corrosion monitoring systems, engineers can predict when maintenance is needed and schedule it at optimal times. This can help to reduce downtime and increase efficiency while also improving safety by detecting potential issues before they become significant problems. As technology continues to advance, it is likely that predictive maintenance will become even more effective, allowing for safer and more reliable underground pipelines in the future.